FRP as a Retrofitting Solution
The use of FRP in repair, strengthening and retrofitting projects is now widespread. Damaged structures can be enhanced and strengthened by using FRP materials. On the basis of deterioration of infrastructure and the need to strengthen structures to meet strict design requirements, in the past two decades, the emphasis on strengthening and repairing structures has become widespread, all around the world. On the other hand, the seismic retrofitting of structures, eFRP applications in repair, strengthening and retrofitting projects is now widespread. Damage structures can be enhanced and strengthened by using FRP materials.
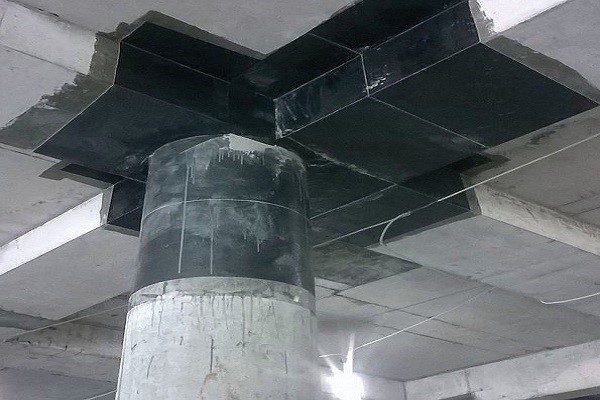
FRP as a Retrofitting Solution for Beams
Unique features of this material, including low weight, high corrosion resistance, high tensile strength and simple execution make it a quick alternative to the traditional methods of strengthening. FRP sheets are installed in different types and with different mechanical properties as an external reinforcement in the needed surface of the concrete members and carry the role of additional load-resisting. Reliability of FRP bonding system mainly depends on the proper transfer of stress from concrete to FRP sheet by common surface. Applying the FRP layer below the beam will change the mode of a bending element from a flexible to fragile state.
Features & Benefits
- Increases flexural strength for both positive and negative moment regions
- Increases shear strength
- Increases stiffness at service loads
- Reduces crack widths for enhanced durability and corrosion resistance
- Delays future corrosion rate by reducing moisture penetration into beam
- No reduction in overhead clearance (e.g. in parking garages)
- Lower cost than conventional methods
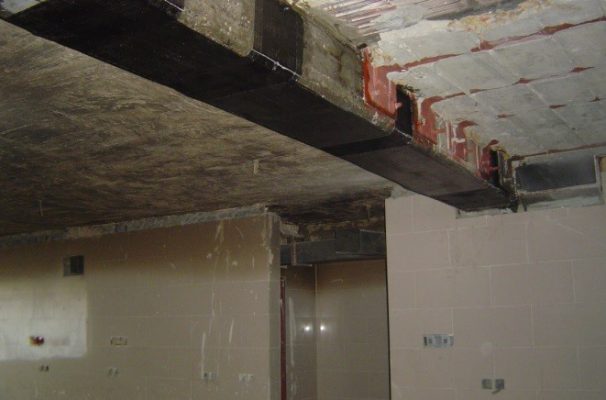
FRP as a Retrofitting Solution for Columns
Strengthening of concrete columns with FRP is a method to reinforce and increase the strength of concrete columns against earthquakes, wear, corrosion, heat, fire, or rehabilitation columns to desired performance. In buildings, rusting, corrosion, increasing living or dead weight and construction errors often lead to weakening of the columns that need to be retrofitted. The use of FRP materials is a fast and cost effective way to retrofit concrete columns. Nowadays, the price of reinforcement of concrete columns with FRP is low compared to traditional methods, and its implementation is easy and inexpensive.
Features & Benefits
- Low time retrofitting
- Low thickness
- Relatively low cost
- Minimal execution restrictions
- Low weight and minimal increase in basic dimensions
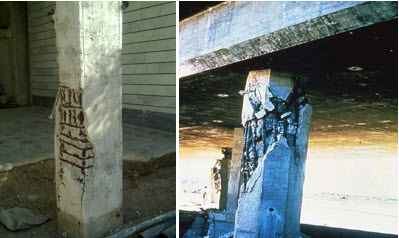
FRP as a Retrofitting Solution for Slabs
To reinforce concrete slabs with FRP, FRP composites can be applied as strips or sheets on tensile surfaces to increase bending strength. A one-way slab with a simple support can be retrofitted by pasting strips or FRP plates at their lower levels in a longitudinal direction. In the two-way slab, retrofit with FRP strips in both directions. Of course, if the slab has an anchor bracket, the FRP strips should also be applied in the upper part of the slab. Also reinforce and refine concrete slabs with FRP to increase the shear capacity of punched concrete slabs around the columns, and strengthen the areas around the openings. The use of CFRP sheets in the tensile region of the slab connection can delay the formation and failure of the shear cracks by increasing the bending strength of the slab adjacent to the column, thereby improving the shear strength of the two-sided joints. In refinement of FRP slabs due to the low thickness of FRP sheets (about 0.05 in. Or 1.3 mm), sheets can easily be covered by floor coverings, and cost reduction and economics of this method lead to its superiority. Compared with other common methods.
Features & Benefits
- Increased flexural strength of one-way slabs
- Increased flexural strength of two-way slabs
- Strengthening and increasing shear strength
- Increasing stiffness and reducing deflections due to service loads
- Increasing ductility
- Corrosion repair and strengthening
- Increasing corrosion resistance
- Economical cost compared to usual methods
- Ease of implementation
FRP as a Retrofitting Solution for Bridge Piling
Recent earthquakes around the world have revealed the weakness of the bridges and the many financial and life losses that resulted from their destruction. In many cases, where the bases are submerged underwater, the implementation of bridge retrofit becomes more difficult. FRP can be used for every type of piles and in any case increases the resistance significantly. Because it do not depend on the type of bridge base and the way it was executed.
PileLaminateTM is a new method based on FRP composite materials for reinforcing the bridge piles, which is provided by Afzir Company. PileLaminateTM is produced by impregnating carbon fiber or glass in resin and then subjecting them to pressure and heat ; the result is a roll in the thickness of about 0.7 mm, a width of 2.1 m and a length of 91 meters. Depending on the layers, PileLaminateTM has 2 to 4 times the strength of steel. These layers can be cut to desired length and then twisted two or more times around the bridge base to cover firm and seamless bridge pile; the distance between the bridge base and PileLaminateTM is also filled with slurry or resin. The crust resulting from the formation of enclosure and the prevention of moisture penetration, almost completely stops corrosion.
Features & Benefits
- Increase axial, shear, and flexural strength of bridges
- Ideal solution is to retrofit the base of a submerged bridge piles in water
- Minimizing the dimensions of the retrofitted bridge pile
- Remove the concrete level repair step before the main refinement process
- Reduced corrosion due to the seamlessness of this method
- High speed of implementation of bridges’ retrofitting
FRP as a Retrofitting Solution for Submerged piles
The predominant use of the submerged piles is in river bridges and offshore platforms. The repetitive drying-wetting cycle will increase the rate of corrosion in steel and concrete of the submerged piles. The most commonly used protecting solution against corrosion is to make a cast from fiberglass and implementing it around the pile and then filling the gap between the cast and pile with resin. These jackets do not increase any structural strength in a damaged pile. In addition, because these casts are not seamless, oxygen and moisture can still reach the surface of the pile and continue to corrode.
PileLaminateTM is a new method proposed by Afzir company is designed to overcome these problems. PileLaminateTM is produced by impregnating carbon fiber or glass in resin and then subjecting them to pressure and heat; the result is a roll in the thickness of about 0.7 mm, a width of 2.1 m and a length of 91 meters. . Depending on the layers, PileLaminateTM has 2 to 4 times the strength of the steel. These layers can be cut to desired length and then twisted around two or more times around the damaged pile to cover a solid, seamless submerged pile; the distance between the pile and PileLaminateTM is also filled with slurry or resin. The crust resulting from the formation of enclosure and the prevention of moisture penetration, almost completely stops corrosion.
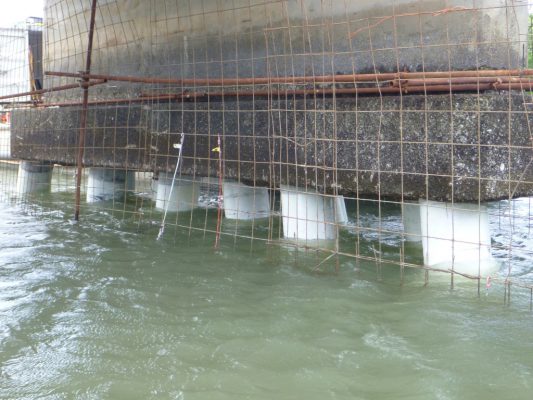
Features & Benefits
- Increasing axial, shear, and flexural submerged piles
- Ideal solution for retrofitting a damaged pile in water
- Minimizing the magnitude of the dimensions of the strengthened piles after retrofitting with the help of polymer composite materials
- Eliminating the concrete level repair step before the main retrofitting process
- Reduced corrosion due to the seamlessness of this method
- High speed execution of submerged piles retrofitting
FRP as a Retrofitting Solution for Walls
The use of FRP (carbon fiber or glass) materials in retrofitting of armed and unarmed concrete walls and masonry walls is widespread. This system is able to increase the flexural and shear strength of the wall, and also prevent the collapse of the walls made of discrete blocks by interconnecting the elements of the block-made walls, and to some extent delaying the movement of the wall surface and hence delaying the failure of these failure modes. . According to valid tests, the seismic behavior of the strengthened walls has improved drastically with this retrofitting system, and also the behavior of these walls against explosive forces has improved significantly. This system can also be used to repair wall defects, replace corroded or removed bars (in order to creating holes in walls for walls, windows, or installations), as well as wall moisture insulation.
Features & Benefits:
- Increasing shear and flexural strength of the wall
- negligible increase in weight of the wall
- Strengthening the entire wall by retrofitting only a fraction of the surface area
- Serves as a waterproofing system
FRP as a Retrofitting Solution for Chimneys
Due to chemicals and gases leaving chimneys, the reinforcement in concrete chimneys are prone to deterioration. FRP products are a unique solution to take care of this problem. FRP sheets of low thickness (approximately 0.05 or 1.3 mm) could be installed on the outer surface of the chimney’s wall similar to wallpapers to strengthen the Chimney.
Afzir engineers will determine the number and orientation of fibers in each layer of the FRP fabric and will provide sealed engineering drawings for such repairs.
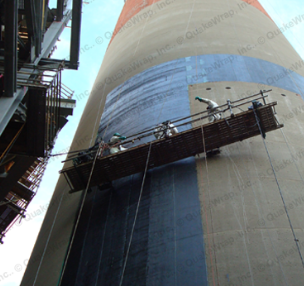
Features & Benefits:
- Increasing bending and shear capacity of the chimney
- Increasing the ductility of the structure of the chimney
- High tensile strength and modulus of elasticity of FRP composites
- High corrosion and acid resistance of FRP composite
- Good connection of the FRP sheet to the various surfaces of concrete and iron and therefore low overlap length and hence lower cost of materials
- Easy transportation due to low weight of FRP composite materials
- More speed and easy execution
- The good price of materials
- Low thickness and weight
FRP as a Retrofitting Solution for Cooling towers
Cooling towers, one of the main components of a thermal power plant, exist into two categories of steel and concrete towers. So far, concrete type has been more attractive to the designers. Repetitive dry and wet cycles result in ideal conditions for corrosion of the structures. Therefore, steel reinforcement bars get corroded very soon, in most cases. In addition, taller cooling towers in nuclear power plants have concrete columns and beams in the base level, which corrode very soon. In this case, retrofitting strategy must account for two important aspects. First, it should be able to compensate the structural damage due to corrosion of the reinforcement and second, is should contain appropriate protection mechanism to reduce the rate of subsequent corrosion. The composite materials of FRP provided by Afzir company are capable to supply both aspects.
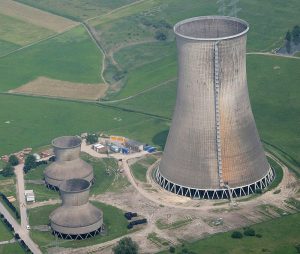
Features & Benefits
- Minimal increase in member size (about 13mm)
- The possibility of finishing the project in the scheduled time due to fast retrofitting rate
- Ideal for spot repair of only damaged areas
- Increase the anti-corrosion resistance of the element by waterproofing it
- FRP will serve as a moisture barrier to protect the beams and columns against future corrosion
- Possibility of painting the finished surface in order to match the original structure
FRP as a Retrofitting Solution for Silos
Grain silos are huge structures used mainly in the agricultural industry. Repetitive dry-wet cycles lead to corrosion of reinforcing steel and cracking of the concrete of these structures. As to the cracks, they may be injected and filled with epoxy. but this solution does not account for the loss of strength caused by corrosion of steel reinforcement. stacking steel plates to the outside of the silos is a traditional solution that is not effective. Because it results in an another problem which is the need for maintenance of the steel plates against corrosion.
FRP offers a great alternative effective technical solution for this problem. Thin (0.05 inch or 1.3 mm) layers of carbon FRP can be bonded to the outer surface of the silo. The use of these layers will lead to transfer the load over a large area and relieve stress concentration points. The FRP will also act as a protective layer that will protect the concrete and steel from corrosion in future. Afzir engineers will undertake the design for these applications and provide engineering drawings for customers.
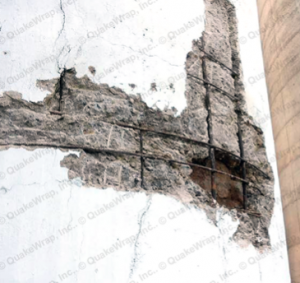
Features & Benefits
- Repairs can be done internally or externally
- Minimal increase in wall thickness (typically ¼ inch (5mm))
- Repairs are fast and often performed while the silo is in service
- Ideal for spot repair of only damaged areas
- FRP will serve as moisture-barrier to protect the tank against future corrosion
- Finished installation can be painted, making it hardly visible
FRP as a Retrofitting Solution for Foundations & Pedestals
Severe environmental conditions in mines, refineries, and coastal and marine areas cause corrosion of in reinforcement bars and cracking in the concrete of foundation. In some cases, improper design, in which the amount of reinforcement bars is not sufficient, may lead to similar problems. In all of these cases, use of FRP Composite Products is an ideal solution for strengthening the foundation and the pedestal. The PileLaminateTM polymer composite product, which is recently introduced, can solve all these problems in a short time and without disturbing the operation.
Features & Benefits
- Increasing axial and shear capacity of foundations
- The FRP will serve as a moisture-barrier, significantly reducing the corrosion rate
- Virtually no increase in foundation size
- Repairs are fast with minimal disruption of service
- Ease of transportation due to low weight
FRP as a Retrofitting Solution for Culvert
Culverts are intersecting structures that are designed to guide surface runoffs and putrid water flowing from the upstream to the downstream and also to protect irrigation channels against these currents. Culvert is an intersectional structure that drains surface currents caused by storms, drainage waters, irrigation sprawls, drains and other excess water from under the road, canal or other facilities and drains the outlet through the predetermined openings.
Corrugated metal pipes and underground channels (culverts) are considered as very important components of highways. Corrosion of culverts is a very common problem in highways which can threat the safety of the highway. Progressive corrosion will lead to local or general collapse of the culvert, eventually. Therefore, strengthening of concrete culverts is of great importance. One of the new methods for strengthening and retrofitting of culvert structures is the use of FRP composites. In all cases, Afzir engineers will recommend the most suitable product for the repair. They will design the retrofit including the number and orientation of fibers in each layer of the FRP fabric and will provide engineering drawings for such repairs.
Features & Benefits
- Repairs are trenchless, requiring zero or minimal excavation
- Minimal increase in wall thickness (typically ¼ inch (5mm))
- Ideal for spot repair of only damaged areas (e.g. joints only)
- Repairs are fast with minimal downtime
FRP as a Retrofitting Solution for Sheet piles & Seawalls
Steel sheet and sea wall piling are often used in foreshore projects. Sheet pilings are materials that provide stability during excavation. The parts of the sheet piles are locked together and can be made of reinforced concrete, steel and timber. Most of the piles are steel sheets. The sea wall is a guarded structure protecting against the waves, tides and tsunami from coastal lines. The changes in the wave of the sea lead to dry-wet cycles resulting in an increase in the rate of corrosion. Mostly, corrosion occurs in the splash zone, which can be defined based on the difference between the lower and upper limits of the sea wave.
The large size of sheet piles and seawalls and the fact that they are partially submerged in water makes their repairs very challenging. Afzir FRP system is an economical solution to such repairs.
Features & Benefits
- Sheet Pile Repair system works on concrete, steel and timber structures
- Lightweight panels lead to fast and economical repair
- Sheet Pile Repair system system will not corrode and requires little maintenance
- Impervious FRP system will significantly lower the corrosion rate
- Finished installation can be architecturally coated
FRP as a Retrofitting Solution for Utility poles
Utility poles are very common structures, that are vital for civil services and a wide range of industries such as power lines and communications. That are usually made of concrete, steel or wood. These structures are prone to corrosion and fatigue based on the material ther were made of it. In this case too, Afzir engineers will recommend the most suitable product for the repair. They will design the retrofit including the number and orientation of fibers in each layer of the FRP fabric and will provide engineering drawings for such repairs.
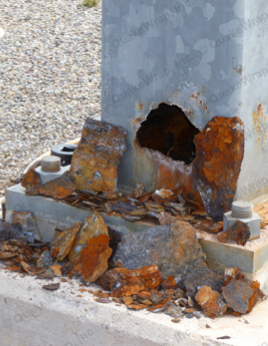
Features & Benefits
- Repairs are fast with no disruption of service
- minimum increase in column dimensions and footprint of the pole
- Repairs are applicable to all type of materials (steel, concrete, timber, …)
- increases axial (tension and compression) and flexurl capacity of columns
FRP as a Retrofitting Solution for Manholes & Access points
Access points usually referred to as “manhole” or “pit” are made in order to get access to buried infrastructure, such as pipes, tunnels, access chambers, and so on. Concrete and brick are common materials for construction of these manholes. These structures are prone to H2S gas and therefore corrosion. Different methods have been used to repair and rehabilitate pits of facilities and access points such as epoxy spray, cement slurry and FRP implementation method.
The company’s solution for improving the wells of the facility and access points is the innovative and cost-effective method of CombPipeTM. CombPipeTM components can be designed with sufficient resistance to any desired dimension and shape to withstand various loads such as traffic and soil pressure.
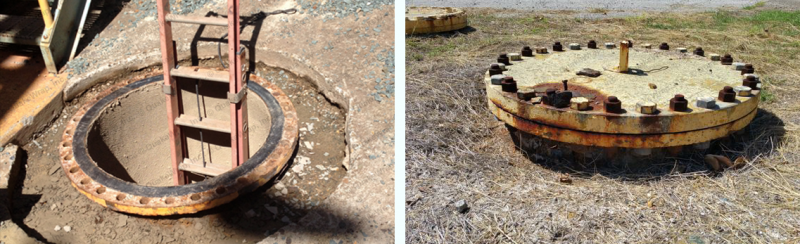
Features & Benefits
- Repairs required minimum excavation only to remove the cone
- Minimal loss of diameter of manhole due to repair
- Repairs are fast with minimal downtime
- CombPipeTM is a polymer composite material that does not corrode.